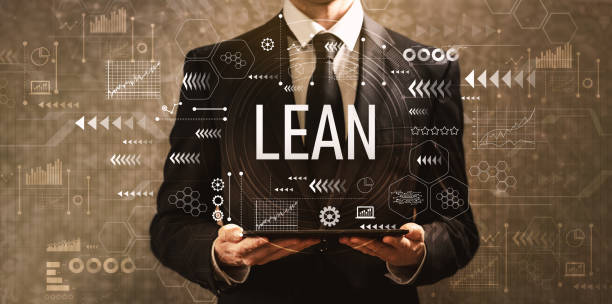
Lean methodology is a powerful approach to streamline operations, reduce waste, and enhance efficiency in various industries. A key aspect of Lean thinking is identifying and eliminating the seven common types of waste, often referred to as the “7 Wastes of Lean.” These wastes include overproduction, waiting, transportation, over-processing, inventory, motion, and defects. Let’sexplore each of these seven wastes and discuss effective techniques to combat them within your organization.
- Overproduction
Overproduction occurs when you produce more than what is currently needed, leading to excess inventory and resource wastage. To combat overproduction, consider implementing the following techniques:
- Just-In-Time (JIT) Manufacturing: Adopt a JIT system to produce goods only when customer demand exists, reducing the chances of overproduction.
- Pull System: Implement a pull system where work or production is initiated based on customer demand rather than a predetermined schedule.
- Waiting
Waiting waste happens when employees or processes are idle due to bottlenecks or inefficient workflows. To address waiting waste, consider the following:
- Value Stream Mapping: Analyze your production processes through value stream mapping to identify bottlenecks and streamline the workflow.
- Balancing Workloads: Distribute workloads evenly to avoid overloading certain areas while others wait for work.
- Transportation
Transportation waste occurs when excessive movement of materials or products is required. Minimize transportation waste with these strategies:
- Layout Optimization: Rearrange the workspace to reduce the distance and time materials or products must travel.
- Cellular Manufacturing: Create work cells that group machines and processes closely together to minimize movement.
- Over-Processing
Over-Processing waste is a result of excessive or unnecessary work beyond what’s required to meet customer needs. Combat overprocessing with the following techniques:
- Standardized Work Instructions: Clearly define standardized work processes to prevent employees from adding unnecessary steps.
- Continuous Improvement (Kaizen): Encourage a culture of continuous improvement to identify and eliminate non-value-added processes.
- Inventory
Excessive inventory ties up capital, space, and resources. Combat inventory waste by implementing these techniques:
- Kanban System: Utilize the Kanban system to regulate inventory levels and replenish only what is needed.
- Supplier Collaboration: Collaborate with suppliers to establish just-in-time deliveries, reducing the need for large stockpiles of raw materials.
- Motion
Motion waste refers to unnecessary physical movement of people or equipment. To reduce motion waste, consider these approaches:
- Workstation Design: Optimize workstations to reduce excessive movements and make tools and materials easily accessible.
- 5S System: Implement the 5S methodology (Sort, Set in order, Shine, Standardize, Sustain) to organize workspaces efficiently.
- Defects
Defects waste arises when products or services do not meet quality standards, resulting in rework and scrap. To address defects, use these strategies:
- Error-Proofing (Poka-Yoke): Introduce error-proofing mechanisms to prevent defects at the source.
- Quality Control: Implement robust quality control processes to catch and address defects early in the production cycle.
Lean methodology is a potent tool for eliminating waste and improving efficiency in your organization. By identifying and addressing the 7 Wastes of Lean – overproduction, waiting, transportation, overprocessing, inventory, motion, and defects – you can streamline your operations, enhance customer satisfaction, and drive growth. Remember that Lean is an ongoing process, and a culture of continuous improvement is key to its long-term success. By implementing these techniques and fostering a Lean mindset, your organization can thrive in today’s competitive business environment.